If and when a crane fails, there can be injuries, loss of life, and high damage costs. Meanwhile, there’s also time lost “on the job” while the crane is taken out of service and repaired or replaced with another one. Oh, and the incident needs to be investigated, too. In the world of construction, where time is money, a crane failure is an upsetting and often a costly occurrence.
Is it any wonder why safety is paramount when working with cranes? And inspections matter? If cranes were never inspected and no one cared about safety, there’d be a lot more crane failures. Like with most industries, failures are not good– they’re avoided at all costs. That said, sometimes cranes fail. Why?
There are several reasons why cranes fail. Here are some of them…
Wires
For starters, consider wires. Yes– wires. Sometimes they can be overloaded or fatigued. Or maybe they’ve deteriorated. Then there’s the possibility of a pre-existing defect. If and when wires are faulty, hook loads (such as cargo) can unexpectedly drop. Cranes can fail due to bad wires.
Parts
Next, consider slew bearings. These bearings need to be used properly for their specified service use. They also need to be monitored during usage as well as inspected before and after they’re in service. If slew bearings do not work as intended, a crane could topple over!
Thirdly, consider sheaves. If shaves aren’t greased, for whatever reason, that could lead to crane failure, including wire wear damage that causes catastrophes on site.
Human Error
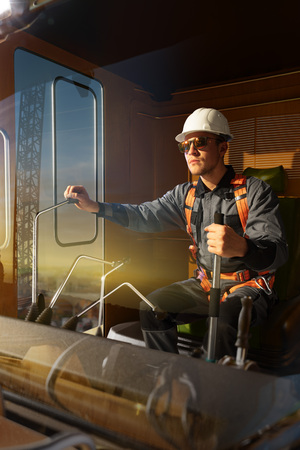
What about crane operators? For whatever reason, if an operator doesn’t do his or her job properly there could be crane failure issues. For example, if a crane operator is literally drunk or high from alcohol or drugs, and he or she is at the controls, watch out– that crane could do something unpredictable in the hands of someone who’s not “all there” mentally.
Now here’s something interesting: what about the times when people assume certain components on a crane are “maintenance-free?” Perhaps people ignore these components, figuring they’re fine. But perhaps they’re not fine– and they should have been properly inspected. Ignoring the inspection and maintenance of certain components can lead to crane failure.
Electrical
Could a crane have electrical faults leading to failure? Yes. A common problem involves sticking or welded contacts. The motor might not stop when it’s supposed to– yikes! Ideally, contacts need to be inspected and cleaned regularly. This is to ensure they’re not sticking. Meanwhile, electrical components can fail– leading to crane failure.
Excess Weight
Cranes also fail if they’re lifting loads that are too heavy for what they’re designed to handle. Cranes are designed for steady and gradual lifts– if there’s a sudden increase/decrease in load, expect problems.
What are some things that need to be checked often, to ensure cranes are working well? If you don’t want a crane to fail, check gearboxes, brakes, bearings, and hoist ropes/chains. Preventative maintenance goes a long way in making sure crane operation is safe.
Astro Crane of New England rents well-maintained hydraulic cranes from 6 to 600 tons. If you’d like more information, please call 978-429-8666 or use the online contact form, here. Astro Cranes are used all over New England, including Maine, Massachusetts, New Hampshire, Vermont, Connecticut, and Rhode Island.